Hot extrusion of high carbon steel cone hollow products
DOI:
https://doi.org/10.20535/2521-1943.2022.6.3.269897Keywords:
direct-reverse extrusion, conical hollow product, finite element method, deformation force, stress, strain intensity, stamping equipmentAbstract
The work is devoted to researching a new method of hot direct-reverse extrusion of hollow conical products from high-carbon steel and determinated parameters for technological design. The considered method makes it possible to obtain in one step hollow products with different wall thickness in height, while the wall thickness in the upper part of the product can be greater than the thickness in the bottom part. The dimensions of the initial workpiece are determined by modeling using the finite element method, which ensures the simultaneous flow of metal in the forward and reverse directions during the process of forming the product, which reduces the deformation force. The use of this method also leads to a decrease in the heating of the deforming tool due to a decrease in the contact area of the deformed workpiece with the tool. The strain rate is determined to ensure the temperature interval of extrusion. The dependencies of the force of extrusion, removal of the punch from the deformed workpiece, pushing the product out of the matrix on the movement of the corresponding tool are established. The final shape and dimensions of the product with the distribution of temperature and deformations were found. For the maximum amount of extrusion force, the distributions of specific forces on the contacting surfaces of the punch, matrix, ejector and stress on the volume of the deformed workpiece were found. According to the obtained data, the technology of direct-reverse extrusion can be developed and implemented on universal press equipment, which has high productivity due to the reduction of the number of stamping steps. The design of the stamp for extruding products of certain sizes with forced cooling of the matrix is given.
References
- E.Y. Semenova Ed., “Horiachaia obъemnaia shtampovka”, in Kovka y shtampovka: Spravochnyk, 4 Vols., T.2. Moscow: Mashynostroenye, 1986.
- L.I. Aliieva et al., “Sposib vyhotovlennia detalei typu hilz”, Pat. 141858 Ukraina, No. u201911074, April 27, 2020.
- V.N. Danchenko, A.A, Mylenyn and V.Y. Kuzmenko, Komp'yuternoe modelirovanie protsessov obrabotki metallov davleniem. Chislennye metody, Dnepropetrovsk: Sistemnye tekhnologii, 2008.
- S.A. Snytko and V.L. Kaliuzhnyi, “Konechno-elementnoe modelirovanie mnogoperekhodnogo formoizmeneniya pri proizvod-stve zheleznodorozhnykh koles”, Vestnik NTUU “KPI”. Mashinostroenie, No. 11, pp. 106–112, 2011.
- DOI: 10.1007/s13191-011-0075-8
- Y.S. Alyev, O.E. Markov and Ya.H. Zhbankov, “Vliyanie operatsii vyvorota pokovki konicheskimi plitami na raspredelenie deformatsii”, Obrabotka materialov davleniem, Kramatorsk: DGMA, 3(24), pp. 64–69, 2010.
- Y.S. Alyev, Ya.H. Zhbankov and L.V. Tahan, “Upravlenie napryazhenno-deformirovannym sostoyaniem zagotovki v protsessakh kovki krupnykh pokovok”, Obrabotka materialov davleniem. Kramatorsk: DHMA, 1(34), pp. 50–59, 2013.
- O.E. Markov, A.O. Sharun and M.S. Kosylov, “Sovremennye sposoby polucheniya tonkostennykh dnishch otvetstvennogo naznacheniya”, Obrabotka materialov davleniem, Kramatorsk: DHMA, 1(44), pp. 115–123, 2017.
- V.L. Kaliuzhnyi and O.S. Yarmolenko, “Zusyllia deformuvannia, napruzheno-deformovanyi stan i temperaturnyi rozpodil u zdeformovanii zahotovtsi pry hariachomu zvorotnomu vydavliuvanni porozhnystykh vyrobiv iz latuni”, Visnyk NTU «KhPI». Innovatsiini tekhnolohii ta obladnannia obrobky materialiv u mashynobuduvannia ta metalurhii, 23(1299), pp. 28–33, 2018.
- V.L. Kaliuzhnyi et al., “Goryachaya ob"emnaya shtampovka polykh izdelii iz vysokoprochnogo alyuminievogo splava s za-dannymi mekhanicheskimi svoistvami”, Zagotovitel'noe proizvodstvo, Moscow, 12, pp. 18–25, 2018.
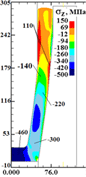
Downloads
Published
How to Cite
Issue
Section
License
Copyright (c) 2022 Володимир Калюжний, Лейла Алієва, Олександр Ярмоленко, Станіслав Ситник

This work is licensed under a Creative Commons Attribution 4.0 International License.
Authors who publish with this journal agree to the following terms:
- Authors retain copyright and grant the journal right of first publication with the work simultaneously licensed under CC BY 4.0 that allows others to share the work with an acknowledgement of the work's authorship and initial publication in this journal.
- Authors are able to enter into separate, additional contractual arrangements for the non-exclusive distribution of the journal's published version of the work (e.g., post it to an institutional repository or publish it in a book), with an acknowledgement of its initial publication in this journal.
- Authors are permitted and encouraged to post their work online (e.g., in institutional repositories or on their website) prior to and during the submission process, as it can lead to productive exchanges, as well as earlier and greater citation of published work